How to Develop and Implement An Effective Force Main Condition Assessment Program
Utilities across the country are facing the reality that many of their collection system assets are near (or beyond) their useful life. The 2017 ASCE Infrastructure Report Card gave Wastewater Infrastructure in the U.S. a score of D+ and there is a $105 billion annual investment gap in water and wastewater infrastructure renewal and replacement.
An increase in force main failures across the country has driven more attention—both industry and public—to these types of failures. Maintaining operations during a force main failure is more challenging than a gravity sewer failure because of the difficult access for installation of temporary pumping or piping and the long distance to the next point of discharge.
Given equal size and flow, failure of a force main asset is generally more critical than a gravity sewer failure from a Consequence of Failure (CoF) point of view—forcing many utilities to answer difficult questions about the condition of their force mains, possible risks, what technologies to use, and budgeting to repair or replace force mains.
Related Topics:
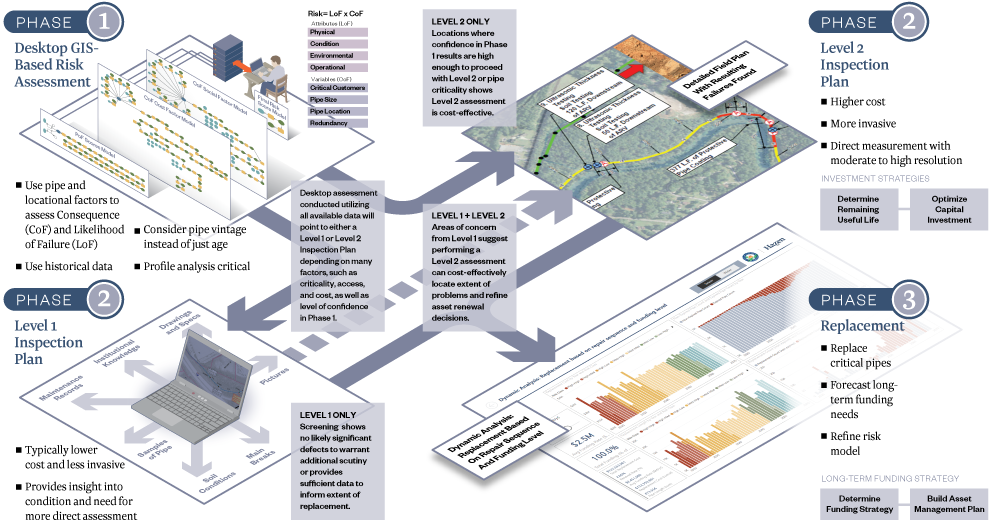
Hazen has successfully utilized a phased, risk-based approach to cost-effectively develop and implement a force main condition assessment program to better inform and justify CIP funding.
Rather than focusing on particular inspection technologies, leveraging existing data and knowledge of why force mains fail are key to developing a cost-effective, risk-based field program.
Understanding Why Pipes Fail
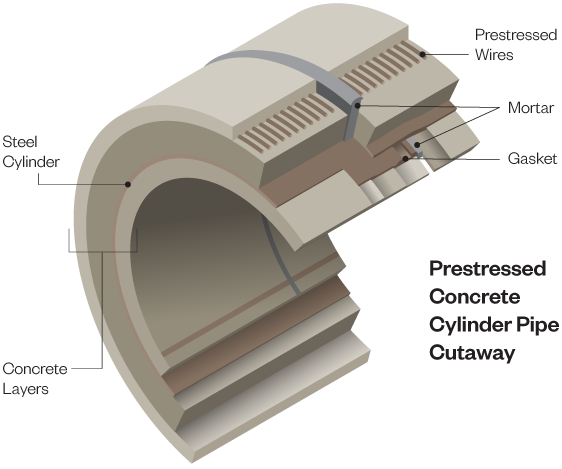
Prestressed Concrete Cylinder Pipe: PCCP pipe is a common material used for force mains due to its ability to handle large pressures at a wide range of diameters. In sewer force mains, the primary causes of failure include corrosion at joints, internal pipe corrosion, and wire breaks. Intrusion of chlorides, sulfates, or CO2 through concrete and into reinforcement or prestressing wires is also a major risk for PCCP.

PVC Pipe: PVC pipe is a common material used for force mains due to its low cost, ease of installation, and ability to resist corrosion. However, this material can fail due to bell failure, over-homing, excessive deflection, cyclic fatigue, or point load failure. PVC pipe failure is also often due to poor installation.
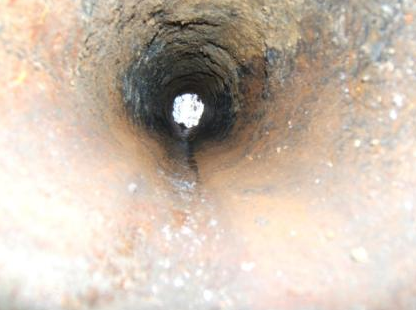
Metallic Pipe: The most common metallic pipe used on force mains includes cast iron, ductile iron, and steel. Cast iron pipe was essentially replaced with ductile iron pipe during the 1960s and 1970s. External corrosion is the primary risk for metallic pipe but it can also fail due to internal corrosion, joint failure, or in the case of cast iron, graphitization. Erosion corrosion can also be found in locations where gritty materials wear the invert and subject the direct metal to sulfide.
Asbestos Cement Pipe: While asbestos cement pipe is not currently used in new pipes, it has been used in the past for force main construction. This type of pipe can fail from carbonation (when dissolved CO2 forms calcium carbonate, which further devolves and leaves the cement matrix), direct corrosion, or poor bedding.
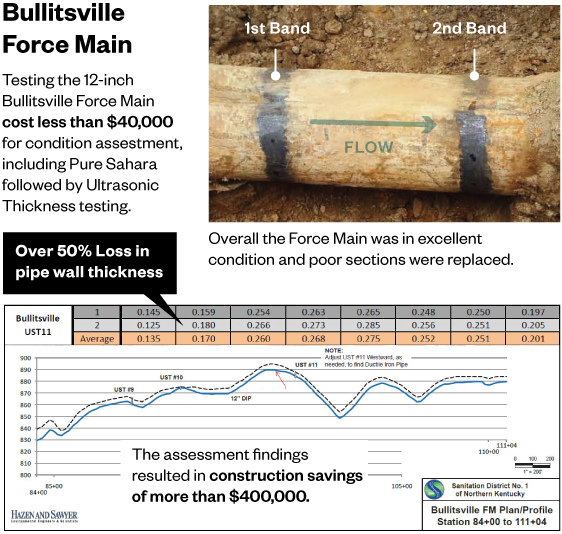
Robust Data Gathering and a Phased Approach Promotes Flexibility
We can interpret assessment results in such a way as to develop a cost-effective force main rehabilitation and repair plan. A key feature of the program is to take a phased approach.
The phased approach considers:
- When condition assessment should occur
- Where it should occur
- What methods should be used
Gravity sewer assessments, by comparison, are always CCTV and/or multi-sensor inspection.
Related Content: Interactive PDF