Large Pipe Inspection Technologies
Pros and Cons of Laser, LiDAR, and Manned Entry
In any gravity sewer collection system, the flows converge to a central trunk sewer or interceptor sewer. Depending on the system’s size, trunk sewers or interceptors are frequently “large diameter pipes.” For the purpose of this presentation, large diameter pipes are considered to be 36-inches and larger. However, this presentation also applies to much larger pipes. The size distinction is based on methods of inspection, pipe materials, and criticality. Pipe material tend to switch from clay, PVC and iron, to concrete, brick or fiberglass reinforced polymer at this size. Inspection also tends to utilize more than traditional closed-circuit TV inspection. Large pipes tend to have a higher criticality as well, since larger areas are served; the consequence of failure is higher; and repairs are more challenging and costly. The decision to repair a large diameter trunk sewer is generally more complicated than repairs of smaller sewers and therefore better condition assessment information and interpretation of the results is warranted.
Related Topics:
Options for Inspections
Inspection technologies are available in both 2D and 3D.
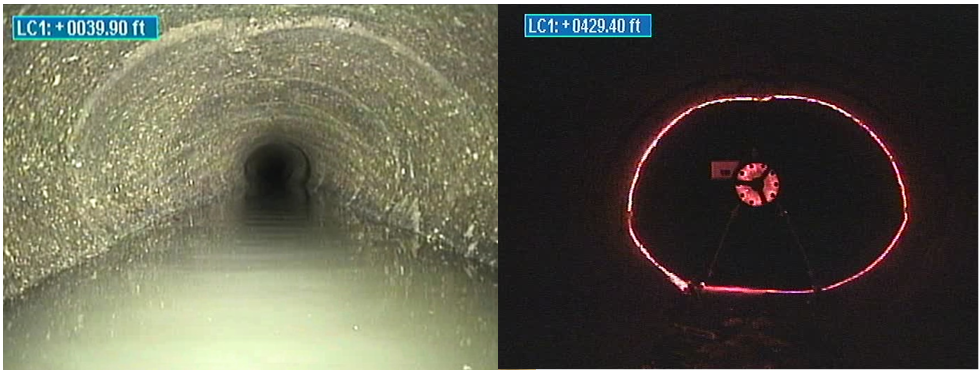
Pipe inspection, or condition assessment, is most commonly conducted by a remotely guided closed-circuit television camera (CCTV) and a trained viewer documenting defects. The documentation of defects has a widely used standard to limit subjectivity of the viewer. There are limitations to this approach, especially with larger pipes constructed of concrete, brick, or stonework, where the most severe defects can be difficult to visually confirm even by a trained observer. Concrete pipe in wastewater applications is subject to biogenic corrosion from hydrogen sulfide gas, which can cause a loss in wall thickness and pipe deformation. Visual inspection of the CCTV may indicate a loss of wall material or pipe deflection but is an unreliable way to accurately quantify these factors. Accordingly, either laser profiling or Light Detection and Ranging (LiDAR) scanning is often used in these applications for a more accurate value.
Laser profiling projects an illuminated “ring” inside the pipe, which is then viewed by CCTV equipment and provides a visual indication of the pipe shape. Either a trained viewer or special software can compare this illuminated “ring” to a known measurement to estimate the internal diameter, and therefore material loss. LiDAR takes this one step further by using light detection to positively measure the internal dimensions. LiDAR can be conducted as two-dimensional (2D) by collecting measured “rings” or “slices” at periodic intervals. Three-dimensional (3D) LiDAR collects measurements in all directions from the LiDAR device. If rehabilitation is being considered for large diameter pipes, highly accurate measurements may be required depending on the type of rehabilitation technology. For example, the degree of deflection (ovality) is a factor in the thickness calculation for cured-in-place pipe (CIPP) liner and shotcrete. In a similar way, the minimum internal dimension is required to be able to slip-line a pipe.
However, both laser and LiDAR inspection have limitations. Through the utilization of these technologies on several projects, these limitations have been documented, and approaches to overcome them have been developed. To process the massive amount of measurement data and produce a useable result, the laser/LiDAR inspection software uses algorithms that make certain assumptions. These assumptions in the algorithm have led to incorrect results in some cases. This presentation will summarize methods to use the raw data along with as-built drawings, spreadsheet calculations, and drafting software to manipulate and correct the data into more usable information. The presentation will also discuss the use of manned entry inspection on several projects, which has its own added value and limitations.