Gasification and Pyrolysis Remove PFAS from Municipal Sludge. But Where Do the Chemicals Go?
A Hazen-led research project could help an industry facing potential new PFAS regulations.
Vincent Carway ↑ sweated as he kneeled on a high platform in the gasification facility. Temperatures inside the mammoth green machine below him regularly hit 2,200 degrees Fahrenheit. He slid a sampling tube into the machine’s top, pulled it out, and tipped its contents—a mix of wet and dried sludge—into a collection jar.
The facility, designed by the company Ecoremedy for the City of Edmonds, Washington, uses a technique known as gasification to turn municipal sludge, meaning the solids removed from wastewater, into clean energy and a valuable solid byproduct.
(Depending on the operating temperature, gasification can produce either a high-carbon material called biochar
or an inert, sand-like material, both of which can be sold for different uses.)
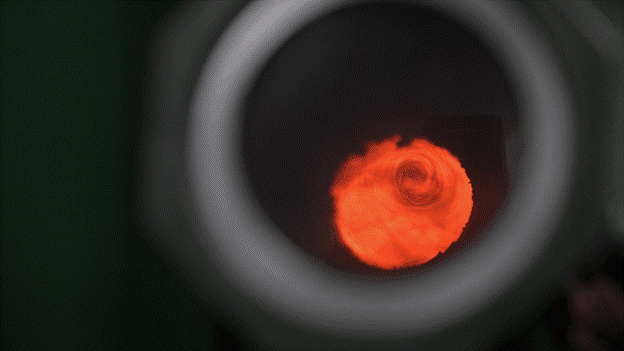
On top of those benefits, recent research has shown that gasification ↑ and a similar process called pyrolysis can remove a group of chemicals called PFAS from the end product.
But the research has also raised a question: Where do the PFAS go? Are they destroyed, or are they simply released into the air?
Carway is part of a Hazen-led team using air samples ↓ as well as solid and liquid samples from the Edmonds facility to answer that question. The results could have industry-wide implications.
“If this project is able to say with some level of certainty that PFAS is destroyed not only in the solids but also in the gases produced by gasification, the industry can start moving towards this technology as a proven way to destroy PFAS in biosolids,” said Hazen Senior Associate Micah Blate, who is leading the work alongside Vice President Mohammad Abu-Orf, the firm’s biosolids practice lead. (The term “biosolids” means sludge that has been stabilized through some form of treatment. Since the material entering the gasification facility in Edmonds has not been treated yet, in that stage it’s referred to as “municipal sludge” or “municipal solids.”)

The Project
Dubbed “forever chemicals” because they don’t naturally break down, PFAS are synthetic chemicals used in countless commercial and industrial products. Some PFAS have been linked to health problems, so the Environmental Protection Agency recently published strict limits for several types of the chemicals in drinking water. It has also designated some of them as hazardous substances.
Because wastewater treatment processes can concentrate PFAS in biosolids, the EPA is also assessing the risks of spreading biosolids over soil. Wastewater utilities rely heavily on that process, called land application, as an affordable way to get biosolids offsite while letting farms recycle the nutrients in them. But it can also transfer PFAS that may be present in those solids to soil and groundwater. If the EPA’s assessment triggers stricter land application rules, utilities may have to find other options fast.
Abu-Orf said gasification (a low-oxygen process) and pyrolysis (which is similar but requires the absence of oxygen) are promising alternatives, since they’ve been proven to remove PFAS from biosolids. But there’s little research on what ultimately happens to the chemicals.
In 2021, his team won a Water Research Foundation (WRF) grant to collect and analyze some of the first data on the fate of PFAS in a full-scale pyrolysis or gasification system for municipal sludge. The research team includes Hazen and Ecoremedy staff, faculty and students from Manhattan College and the University at Buffalo, and the air sampling company Mostardi Platt.
The grant—part of WRF’s Tailored Collaboration Program—matched funds from the organization with contributions from utility partners, including AlexRenew, Massachusetts Water Resources Authority, Middlesex County Utilities Authority, and Portland Water District. Hazen also provided funds, and Ecoremedy covered a portion of the air testing costs.

The Facility
While the team is still analyzing the samples, the sampling work was completed at the Edmonds facility ↑ in March. At the time the team was ready to begin sampling, it was the only gasification or pyrolysis plant for municipal solids in the U.S. that was up and running at full scale. Abu-Orf said finding a full-scale facility was critical:
“Researchers can control conditions in the lab, but when you’re testing at a full-scale plant, you’re at the mercy of real-world conditions.”
Ecoremedy President and Chief Technology Officer Dave Mooney ↓ said the company didn’t start out focused on municipal sludge. Years ago, he was designing systems that could generate energy from wood waste when he got a call from some turkey farmers. They wanted something similar for turkey manure.

“Through the process of trial and error, we invented the Ecoremedy process,” Mooney said. “We’ve been gasifying animal manures for about 20 years. So this technology isn’t new. It’s just been newly introduced to the municipal sector.”
Besides uncertainty about PFAS, wastewater utilities in the U.S. are seeing an increase in the costs of beneficially using or disposing of biosolids, and growing pressure to reduce greenhouse gas emissions from those processes. They’ve taken notice of gasification and pyrolysis because both are cleaner and more energy-efficient than some traditional thermal treatment options. The system Ecoremedy designed for Edmonds replaced an old incinerator.

The Gasification Process
Ecoremedy’s gasification system uses a patented process called Fluid Lift Gasification™. It works like an air hockey table: A mix of wet and dried biosolids enters the chamber of the gasifier ↑, where it’s lifted over a perforated plate by air pumped up through the holes. The suspended mix moves slowly through the chamber, which is heated to upwards of 1,600 degrees Fahrenheit.
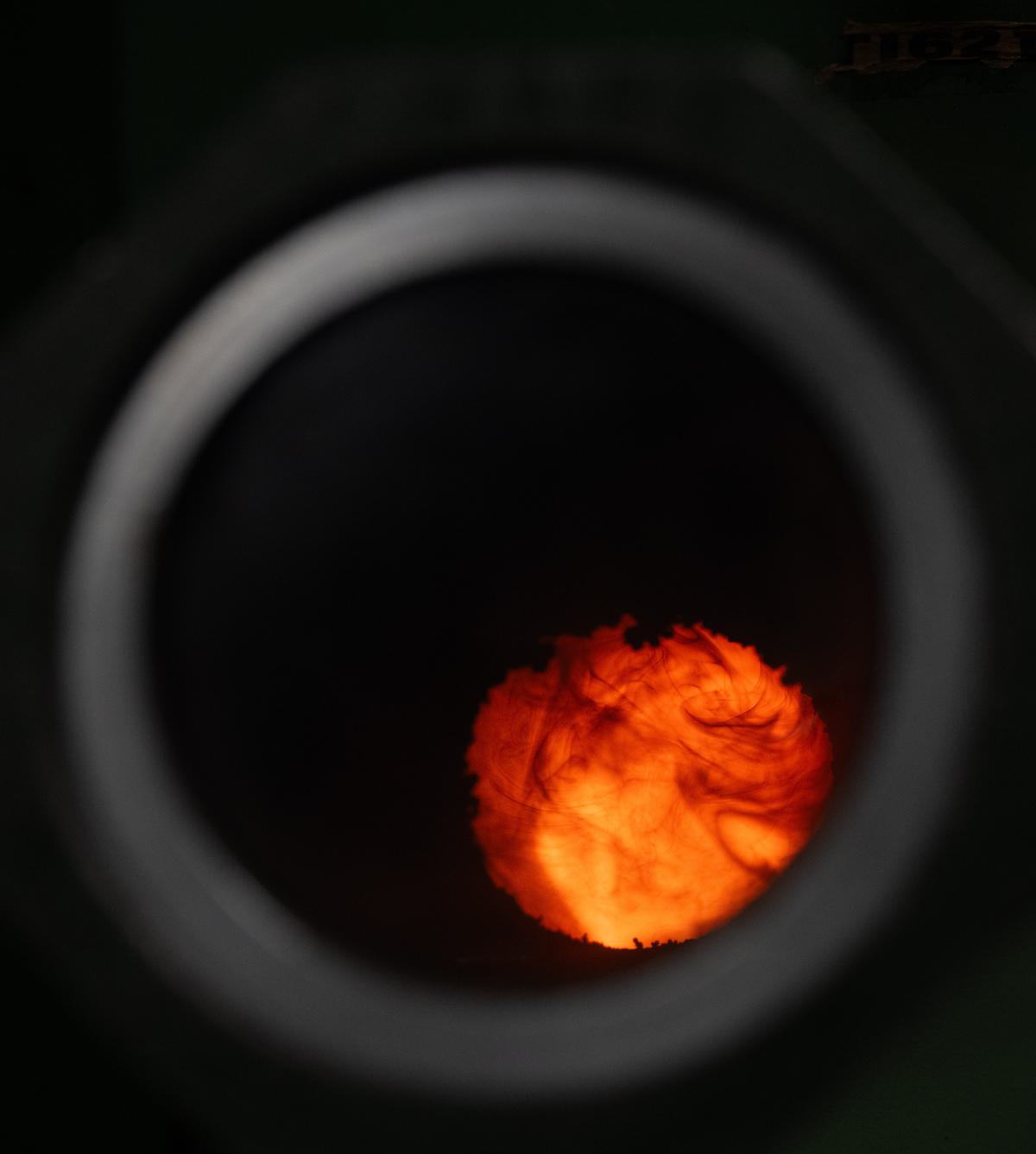
Oxygen levels are kept low, so instead of burning, the biosolids release volatile gases called ← syngas (the dark vapors visible through one of the sight glasses). The syngas is burned up at even higher temperatures, and with much more oxygen present, in a thermal oxidation unit housed in the same machine.
Meanwhile, the remaining solids ↓ (shown through the other sight glass) are funneled into a collection bin.

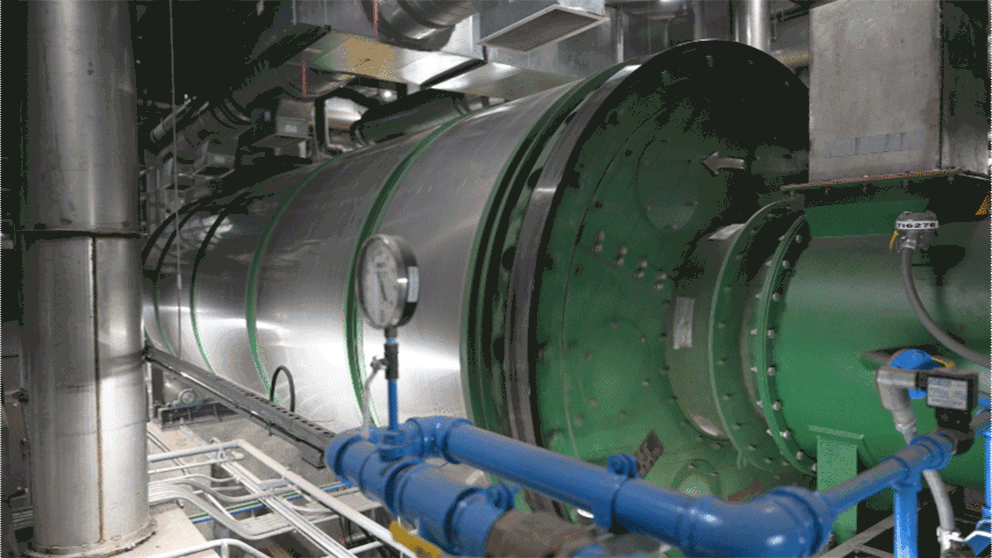
Abu-Orf said the EPA considers gasification a cleaner treatment option than incineration because of the benefits it generates. For example, Ecoremedy uses a rotary drum dryer ↑ to produce dried, high-quality solids that can be land applied or mixed with wet sludge and fed into the gasifier. Heat generated from burning the syngas powers both the dryer and gasifier, reducing the amount of fossil fuel required to run the system.

The solid byproduct from the gasification unit is also 95% lower in volume than the sludge coming into the plant, dramatically lowering how much fuel is needed to truck it away. Mooney said Ecoremedy’s byproduct can be used as a sand-like construction material ↑ and energy source, or as a high-carbon fertilizer.
“And we know gasification and pyrolysis remove PFAS from this kind of sludge,” Abu-Orf said. “But where does the PFAS go? PFAS only get destroyed at temperatures above 1,850 degrees Fahrenheit, and gasification and pyrolysis don’t get that hot. Thermal oxidation of the syngas can go up to 2,000 degrees Fahrenheit. That’s where we believe it can be destroyed.”
The Testing
When Hazen asked Ecoremedy about testing the Edmonds gasification system for PFAS, the company was already planning to test air emissions from the system for permitting purposes. Mooney said it made sense to add PFAS to the mix.
The testing involved more than air samples, however. Gasification is a multi-step process, and Abu-Orf said it was key to collect samples from points throughout the process to confirm which step could be destroying PFAS.
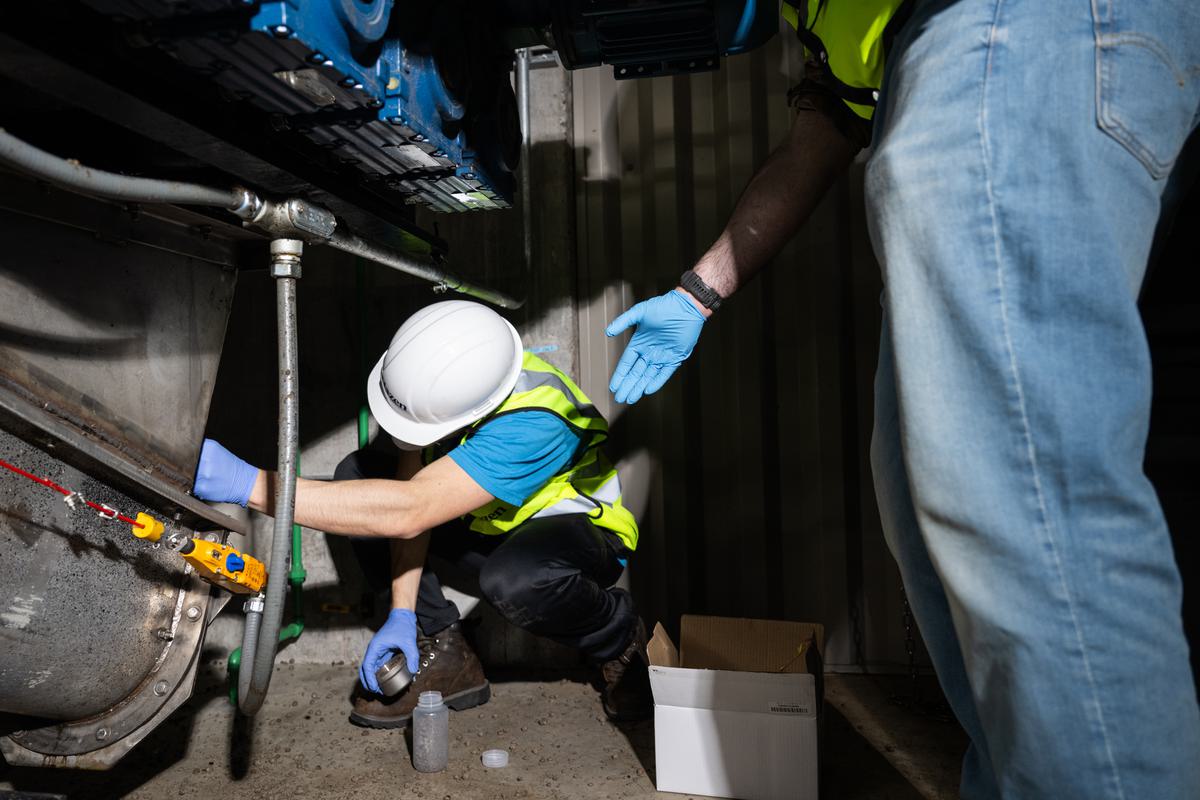
Vincent Carway and Jonathan Antle, students at Manhattan College and the University at Buffalo, respectively, helped the team collect samples of solids and liquids from various steps.

That included samples of wet
sludge on their way to the mixer…

…the mix of wet and dried solids, some headed for the dryer and the rest headed for the gasifier…
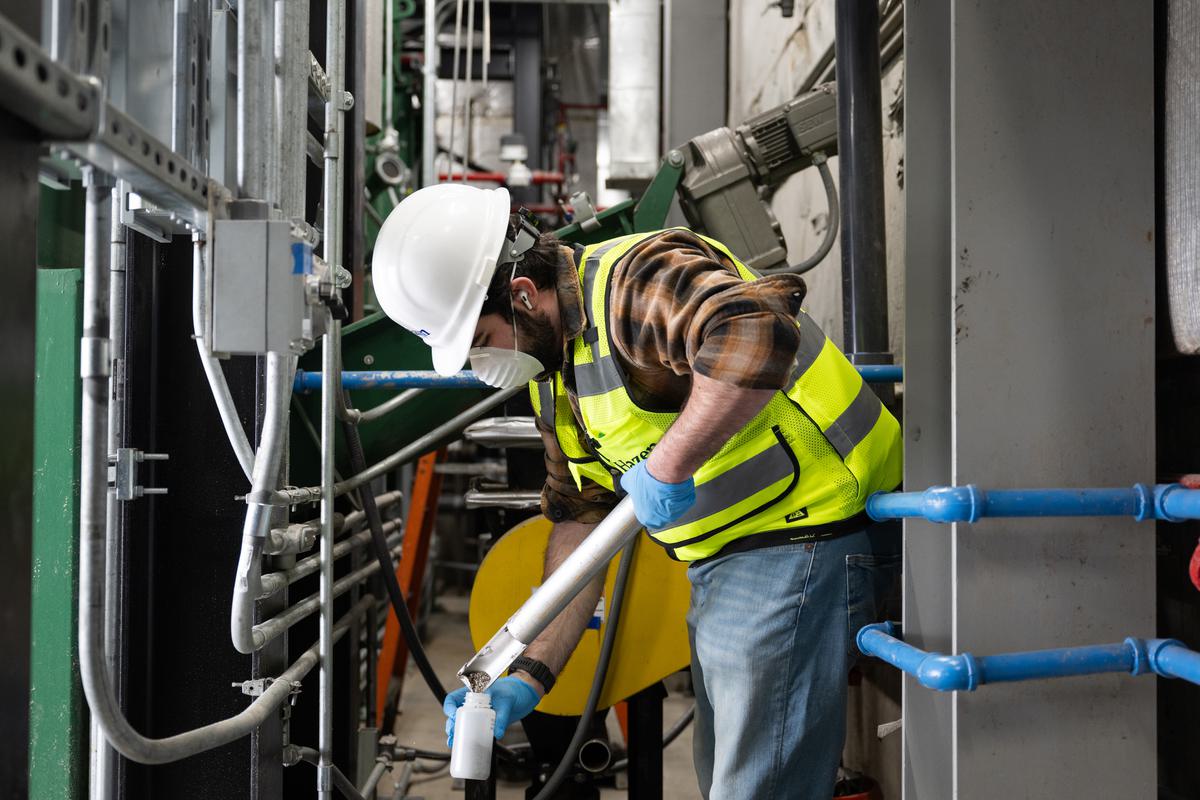
…and solid byproduct exiting the gasifier.

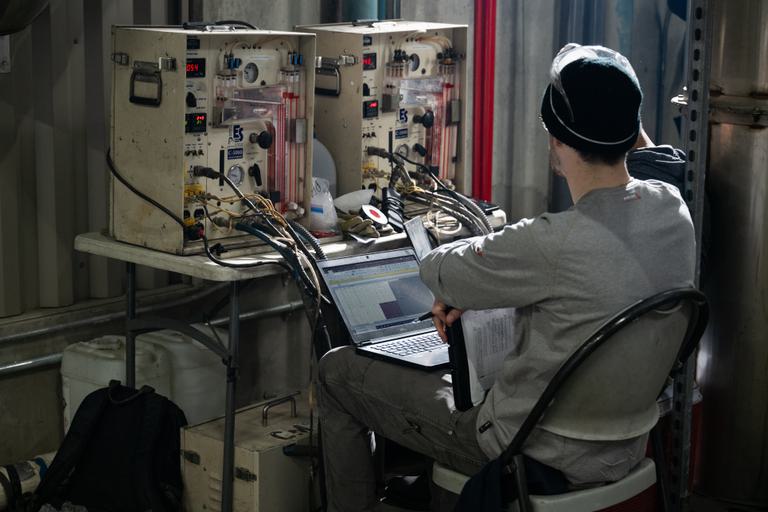

For the air samples, the company Mostardi Platt inserted sensors from an air sampling unit ↗ into the facility’s external air stack. Their staff monitored ↖ the sampling device while it siphoned air into glass containers ↰, which were submerged in an ice bath that condensed the air into liquids.
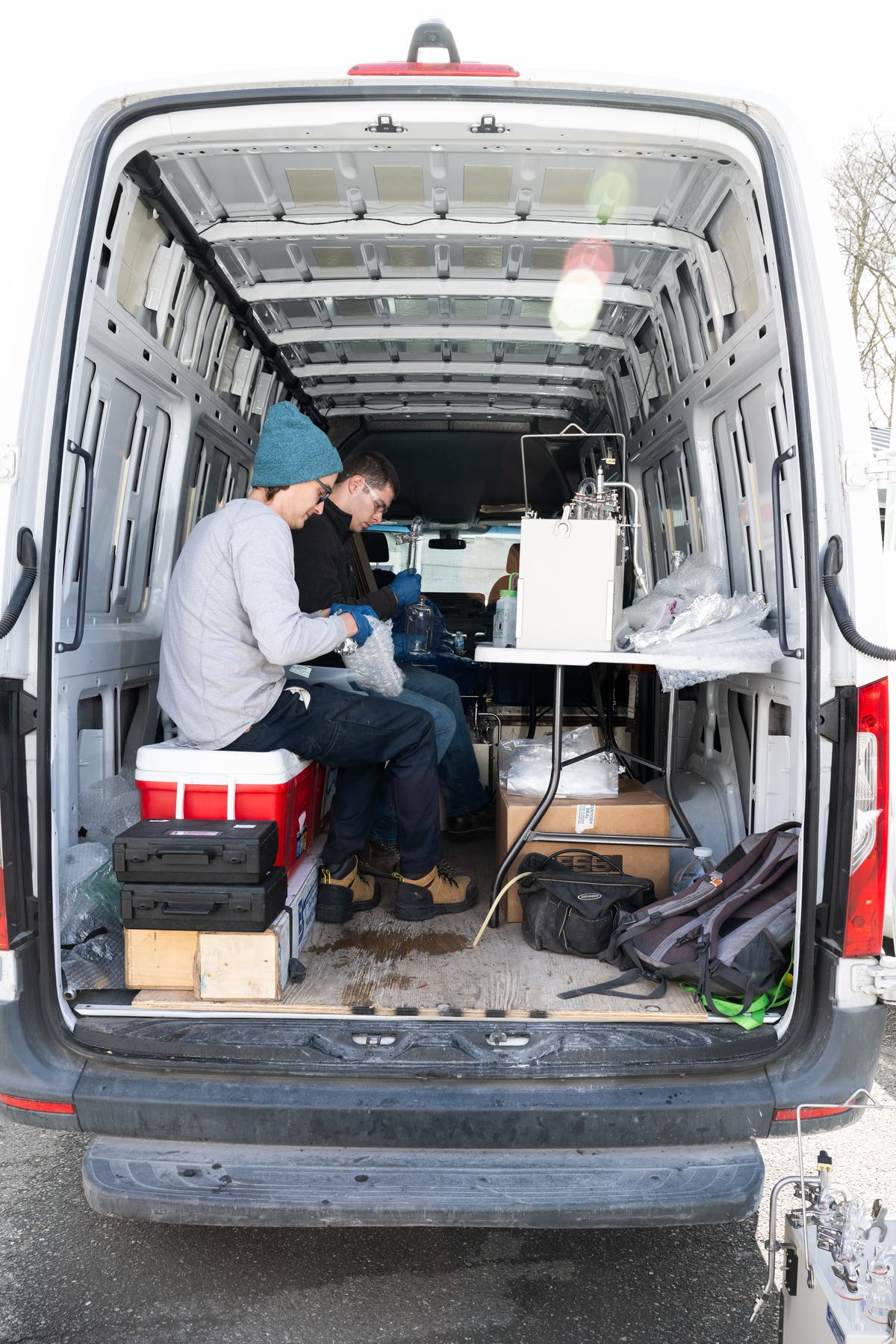
The samples from the air emissions were carefully packed up in Mostardi Platt’s van ← ...
... while Hazen worked with the students to pack up the samples ↓ of solids and liquids.

The Analysis
Mostardi Platt is now analyzing the air samples for PFAS and other key metrics, while faculty and students at Manhattan College and the University at Buffalo are analyzing the solid and liquid samples. Hazen is calculating the system’s total energy inputs and outputs. Once all the data is finalized, the firm will also compare the total startup and operating costs of the gasification system to the costs of more conventional treatment options.
Carway ↓ has since finished school and is preparing to join Hazen full-time. He said he’s grateful for the chance to contribute to the project and collect samples onsite, after spending most of his training time in labs.
“This was a really cool experience with a state-of-the-art technology to remove PFAS,” he said.

Since prior tests have proven that gasification can destroy PFAS, Mooney said he’s hopeful the results from the Edmonds plant will show at least partial destruction. But even if not, he said, the data will offer a crucial “starting point” for the industry. Abu-Orf echoed his high hopes.
“PFAS follow a cycle. They go from households and industries into the sewer system and the treatment plants. A very small amount goes into the effluent—most goes to the biosolids,” Abu-Orf said.
“So if we can destroy PFAS in biosolids before it’s land applied, what we’ve done is break the vicious cycle of PFAS in the environment.”
Photos by Chona Kasinger for Hazen