Membrane Pilot Yields a Year’s Worth of Data, Training, and Buyer’s Confidence
Hazen helped a Tennessee utility learn how to run a new ultrafiltration system while ensuring the equipment could handle a wide range of conditions.
At a Glance
- Hazen led a highly customized ultrafiltration pilot for Columbia Power and Water Systems. The pilot gave staff a year of hands-on experience with a new technology and let them see how the system responded to a wide range of water quality conditions and operational challenges.
- The pilot met all key requirements, including turbidity (a measure of cloudiness used to indicate potential pollution) that never exceeded 0.05 nephelometric turbidity units.
- Pretreatment tests showed that the best coagulant for the membranes was one the plant was already using for its conventional filtration system, and that the plant could further optimize membrane performance by adjusting the pH of the feed water or the chemicals used in daily cleaning.

Scott Alpert specializes in planning, designing, and optimizing conventional and advanced treatment processes, including membrane filtration systems.
Related Topics:
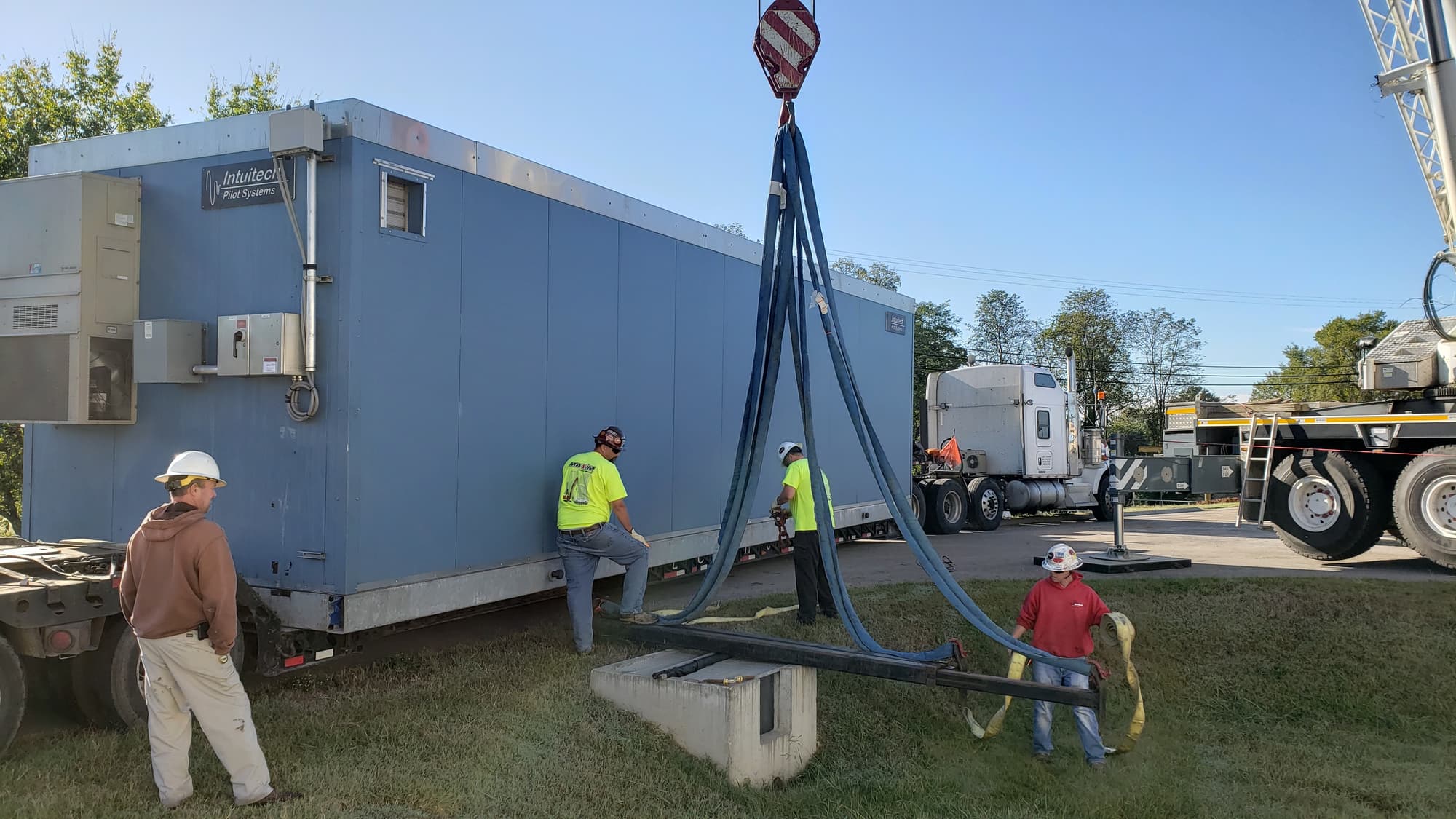
(Above) The pilot was installed near CPWS' existing treatment plant so raw water could easily be piped to it. (Top) Inside the pilot, which contained pretreatment and ultrafiltration systems made by two different manufacturers.
Tennessee’s Duck River is “flashy”—meaning storms can trigger dramatic spikes in its flow. Its water quality can change just as quickly. And depending on the season, water temperatures can range from below 40 degrees Fahrenheit to more than twice that figure. All those variations can make the water challenging to effectively treat. Columbia, a fast-growing city south of Nashville, depends on that finicky river for drinking water.
Columbia Power and Water Systems (CPWS) needed to expand its drinking water treatment capacity and wanted to try ultrafiltration (UF), a kind of membrane technology, for the new treatment trains. UF systems filter water through bundles of hollow, porous fibers. They’re largely automated, tougher for particulates and pathogens to get through than conventional systems, and highly reliable regardless of source water conditions.
But given the Duck’s fluctuations—and the fact that staff were new to UF systems—CPWS wanted to be certain it was a good move. The utility also wanted help determining the best pretreatment chemicals for a UF system. Hazen was hired to design and run a yearlong pilot.
The Pilot Process
CPWS didn’t have room for the pilot in its existing water treatment plant, so we found a unique setup: a shipping container from Intuitech that held both a pretreatment pilot designed by Intuitech and a UF pilot by Veolia Water Technologies and Solutions.
After setup and training, CPWS staff ran the pilot, but Hazen and Veolia monitored it remotely and met with utility staff each week to explain the data and discuss next steps. Our team was also frequently onsite. We tested how the system responded to a wide range of water quality conditions, three pretreatment coagulants, adjustments to other chemicals and cleaning techniques, and stress tests such as shutting off the coagulant supply. At the end of the pilot, we also packaged all the findings into a finished report.
The Results
- Across all scenarios, the turbidity of the filtered water never exceeded 0.05 nephelometric turbidity units, a critical requirement for the system. The pilot also met all other key requirements, from pathogen removal criteria to minimum cleaning frequency.
- Testing showed that the best coagulant was the one the plant was already using in its conventional filtration system, and that the membranes could also benefit from adjusting the pH of the raw water or the chemicals used in daily cleaning.
- Staff learned how to handle the system through all four seasons and a wide range of scenarios. They’re ready to handle the full-scale system that’s now in the works.